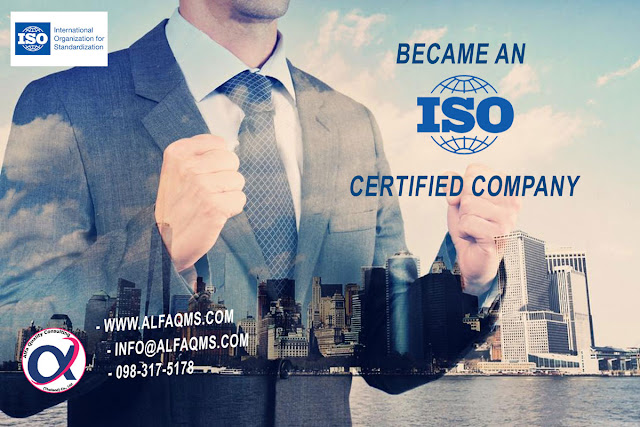
ISO 9000 was first published in 1987 by ISO (International Organisation for Standardization).[11] It was based on the BS 5750 series of standards from BSI that were proposed to ISO in 1979.[12] However, its history can be traced back some twenty years before that, to the publication of government procurement standards, such as the United States Department of Defense MIL-Q-9858 standard in 1959, and the UK's Def Stan 05-21 and 05-24. Large organizations which supplied government procurement agencies often had to comply with a variety of quality assurance requirements for each contract awarded which led the defence industry to adopt mutual recognition of NATO AQAP, MIL-Q and Def Stan standards. Eventually, ISO 9000 was adopted as a suitable option, instead of forcing contractors to adopt multiple - and often similar - requirements.
Reasons for use
The global adoption of ISO 9001 may be attributable to a number of factors. In the early days, the ISO 9001 (9002 and 9003) requirements were intended to be used by procuring organizations, as the basis of contractual arrangements with their suppliers. This helped reduce the need for "supplier development" by establishing basic requirements for a supplier to assure product quality. The ISO 9001 requirements could be tailored to meet specific contractual situations, depending on the complexity of product, business type (design responsibility, manufacture only, distribution, servicing etc.) and risk to the procurer. If a chosen supplier was weak on the controls of their measurement equipment (calibration), and hence QC/inspection results, that specific requirement would be invoked in the contract. The adoption of a single Quality Assurance requirement also lead to cost savings throughout the supply chain by reducing the administrative burden of maintaining multiple sets of quality manuals and procedures.

A few years later, the UK Government took steps to improve national competitiveness following publication of cmd 8621, and Third Party Certification of Quality Management Systems was born, under the auspices of the National Accreditation Council of Certification Bodies (NACCB) which has become the United Kingdom Accreditation Service (UKAS) .

In addition to many stakeholders' benefits, a number of studies have identified significant financial benefits for organizations certified to ISO 9001, with a 2011 survey from the British Assessment Bureau showing 44% of their certified clients had won new business.[14] Corbett et al. showed that certified organizations achieved superior return on assets[15] compared to otherwise similar organizations without certification.[16] Heras et al. found similarly superior performance[16] and demonstrated that this was statistically significant and not a function of organization size.[17] Naveha and Marcus claimed that implementing ISO 9001 led to superior operational performance in the U.S. automotive industry.[18] Sharma identified similar improvements in operating performance and linked this to superior financial performance.[19] Chow-Chua et al. showed better overall financial performance was achieved for companies in Denmark.[20] Rajan and Tamimi (2003) showed that ISO 9001 certification resulted in superior stock market performance and suggested that shareholders were richly rewarded for the investment in an ISO 9001 system.[21]
While the connection between superior financial performance and ISO 9001 may be seen from the examples cited, there remains no proof of direct causation, though longitudinal studies, such as those of Corbett et al. (2005)[16] may suggest it. Other writers, such as Heras et al. (2002),[17] have suggested that while there is some evidence of this, the improvement is partly driven by the fact that there is a tendency for better performing companies to seek ISO 9001 certification.

The mechanism for improving results has also been the subject of much research. Lo et al. (2007) identified operational improvements (e.g., cycle time reduction, inventory reductions) as following from certification.[22] Internal process improvements in organizations lead to externally observable improvements.[23][24] The benefit of increased international trade and domestic market share, in addition to the internal benefits such as customer satisfaction, interdepartmental communications, work processes, and customer/supplier partnerships derived, far exceeds any and all initial investment.
Thanks for this. I really like what you've posted here and wish you the best of luck with this blog and thanks for sharing. ISO certification
ReplyDeleteThanks for given detail information to me. keep posting like this. iso-22000-internal-auditor-training
ReplyDeleteI found your blog and it was really useful as well as informative thanks for sharing such an article with us. We also provide services related to ISO 50001 Certification
ReplyDeleteThanks for sharing this. It is really informative and useful.
ReplyDeleteiso 50001 eğitimi